Olvasási idő: 3 perc
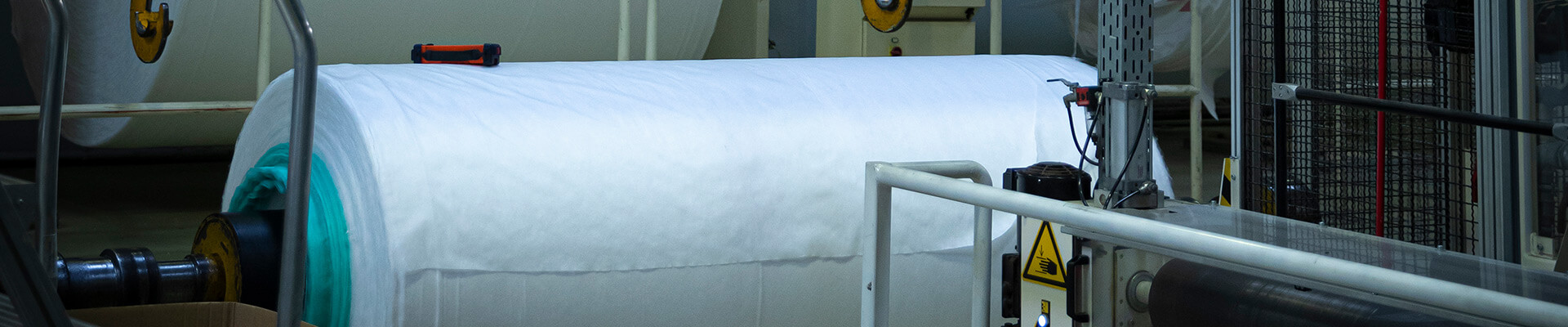
There is a wide range of application areas for these nonwoven / film composite materials. These are, for example, breathable textile backsheets for hygiene articles (diapers, sanitary napkins, panty liners), breathable products in the construction sector (roof underlayments, breathable house wraps, floor protection materials), barrier films in the construction sector, breathable protective clothing in the industrial and medical sector, to name but a few to call.
Traditionally, these composite materials used to be manufactured from the prefabricated nonwoven and film components in a separate joining process. This meant that a total of 3 independent processes and the associated costs were necessary to manufacture the composite material. As a rule, additional logistics costs were incurred for the transport of nonwoven and film webs to the manufacturer of the composite material. The first step in optimizing costs was to coat the film directly with the film on the roll of nonwoven already separately pre-fabricated and fed in by unwinding. This saved one process step and the associated logistics costs. The next logical step is the integration of nonwoven and film production into one process. This represents the most cost-effective variant in the production of the non-breathable composite materials.
When producing breathable materials, the film component must ideally be stretched in both the machine direction (MD) and cross-machine direction (CMD). By varying the stretching, the level of breathability of the film or the composite material can then be set in a targeted manner. The integration of this stretching process represents a technical challenge, but offers a number of economic and process-related advantages that enable the development of cost-effective and application-specific composite materials.
In the Linopore technology, the basic processes, the BICO spunbond technology and the cast process for film production, provide the optimum flexibility for determining the quality features with regard to the required properties of the respective application. This means that a wide range of alternative raw materials and their associated properties can be used in the manufacturing of both composite components. With the BICO spunbond process it is possible to run the carrier fleece with different polymer combinations and thus to match special quality parameters to the requirements of the application area. Here, for example, either PP, PE or PET, but also biodegradable polymers can be used. With the special cast technology and the variably usable application and connection technology, special quality-relevant process parameters can be set during the coating itself.
After the film coating, the MD and CMD stretching of the composite material takes place. Here, the level of stretching can be adjusted in a targeted manner in both process steps and the quality parameters with regard to the physical properties and the level of breathability can be set in accordance with the application. It is particularly important to emphasize that the tensile strength level for a given weight per unit area is higher than that of competitor products, since the entire web, including the nonwoven component, is stretched and the individual fibers thus achieve greater strength. Another advantage is the width of the produced web: here a roll width of up to 5 meters can be produced inline. This means that special widths can be produced without glue seams, such as those required e.g. for prefabricated houses.